The patent-pending 265 CarbonFlex™ Printer Applicator is engineered to apply one or two labels to shipping cases, shrinkwrapped trays, or pallets.
The 265 also boasts these robust features, collectively not found in other systems:
• When installed in nose-up or nose-down orientation, labels are printed along the narrower dimension, meaning more labels available per roll and less overall time for replenishment.
• Barcodes are printed and applied in the preferred orientation, providing the best print quality and less chance of chargebacks from retail companies.
• The 265 has extended reach over the conveyor – reducing the need to change product handling.
• The 265 is all-electric, reducing expenses by not requiring compressed air.
• The 265 is equipped with an Allen-Bradley Micro850 PLC with Ethernet/IP & Modbus communications.
At ID Technology, we genuinely understand material handling and end-of-line packaging. The 265 labeling system with CarbonFlex is designed to be more tolerant of less-than-perfect product presentation than other applicator types, making it the perfect solution for many secondary packaging or pallet labeling automation applications.
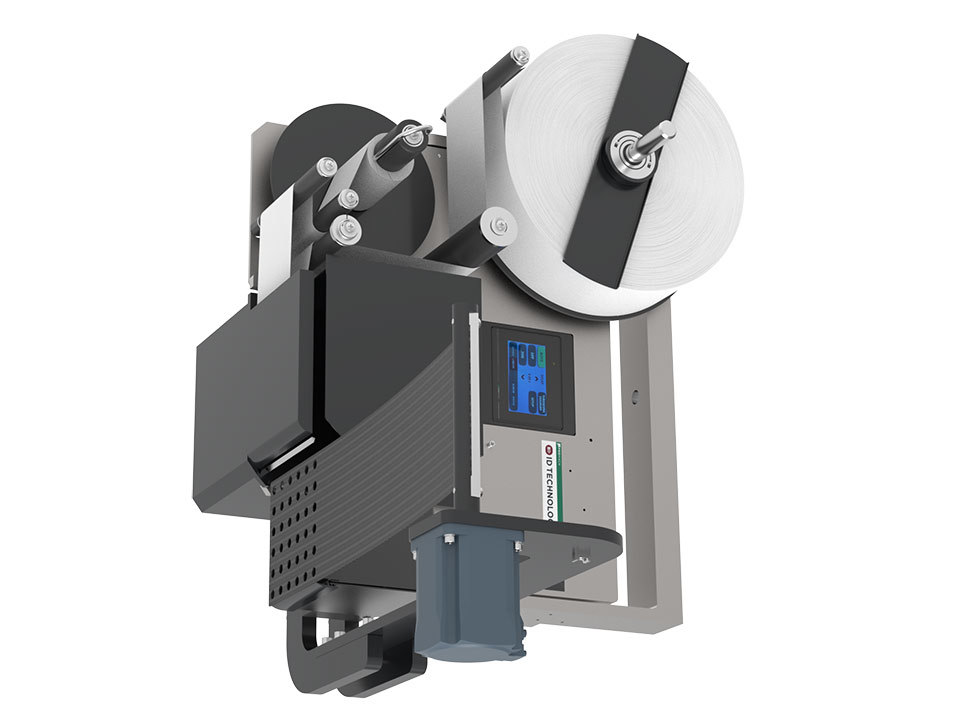
Product Overview
Engineered for Speed & Accuracy
With our patent-pending CarbonFlex™ technology, the 265 decouples the print speed from the applicator speed. Ultimately, we print slower and apply faster. Simultaneously. This means we print the best possible barcode quality, separate from the label’s application rate requirements.
- The 265 prints labels/barcodes at an optimum speed for increased quality and readability. Better scans translate to fewer rejections down the line.
- Designed to be easy to install and to reduce operating costs, the 265 is all electric in operation; no compressed air is needed.
The servo-controlled carbon fiber label application blade is flexible, allowing it to conform to the package position on the conveyor.
The CarbonFlex applicator is less dependent on good product handling than other systems - producing excellent labeling quality, even if the product handling is not perfect.
- To boost your throughput, integrate two 265 systems in tandem and achieve zero downtime in your operations.
Engineered for Safety
Several key features ensure safe interaction with an operator and live operations when the 265 requires service, maintenance, or label roll changes.
- If used with our service stand, the 265 swings away from the conveyor – and automatically switches offline when rotated – to provide safe, unobstructed access for operators.
- No pinch points from reciprocating parts - the servo control instantly stops the applicator blade movement when it comes in contact with anything unexpectedly.
Engineered for Productivity
Designed with operators in mind, the 265 high-speed case, tray, and pallet labeling automation system is engineered to maximize productivity.
- The touch-screen display is designed to be simple for routine tasks and has in-depth diagnostics to help maintenance staff.
- When configured in Nose-down or nose-up orientation, the 265 prints labels along the narrow dimension, equating to having twice as many labels available per roll and reducing the number of label changeovers.
- Barcodes are printed and applied in the preferred orientation, meaning there is no need to slow your rate (or stop altogether) to apply labels.
- The 265 comprises modular components for easy and efficient service and maintenance when required.
- The optional integrated barcode scanner provides barcode validation immediately after label application for even greater simplicity.
Solutions for:
Senior Leadership
Your Challenges:
- Improved productivity in your operations.
- Reduce unnecessary expenses from chargebacks due to poor barcode quality.
Our Solutions:
- Faster than competitor systems - when applying two labels to a package, one 265 can often replace two legacy machines.
- Application speed matches line rate (up to 200 ft/min or more), so you label more product.
- Utilization of two 265s in tandem provides a Zero Downtime solution.
- Barcodes are printed at ideal quality due to printing in the short direction. Optional camera verifies barcode readability immediately after label application.
Operations Management
Your Challenges:
- Downtime due to increased operator interaction with labeling systems.
- Reduction of utility costs.
- Replacement of inkjet solutions that yield poor quality barcodes or inability to imprint on shrink-wrapped trays.
- Minimal floor space available for labeling system/reach to the product.
- Implementing the accurate product handling that other labeling systems demand can be challenging.
Our Solutions:
- Since labels are printed in the short direction, the system yields more labels per roll and requires fewer stops for replenishment = less downtime.
- The system is all-electric, so no compressed air is needed, reducing your overall operating costs.
- Thermal Transfer or Direct Thermal label imprint options provide better quality barcodes (and inkjet not applicable for shrink-wrapped trays).
- Compact footprint, with the ability to reach up to 6" across the conveyor.
- While excellent product handling is better for any labeling operation, the 265 system is more tolerant of package misalignment than other applicator types.
Operators & Technicians
Your Challenges:
- The number of label changeovers that occur during a shift, leading to increased downtime.
- Complex maintenance or service of the label applicator.
- On-the-job injuries due to system complexity or interaction with the system in close proximity to conveyor lines.
- Preventative maintenance notifications not allowing proactive maintenance.
Our Solutions:
- Less need for label changeovers since more labels are available per roll = less downtime.
- System features modular components for ease in maintenance or parts replacement.
- No reciprocating parts or pinch points.
- The carbon fiber applicator blade is designed to be totally safe and reverses direction on and unexpected contact.
- Optional barcode camera alerts you when printhead service is needed.
Contact an ID Technology Account Manager
Ready to improve your production output and operational efficiency? Contact an ID Technology account manager today to learn how our labeling and coding automation solutions will increase your throughput and improve your bottom line.